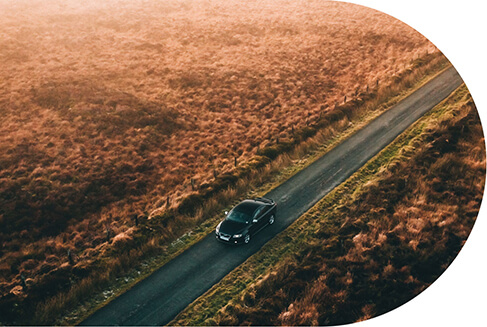
The Electrical Issue - Mark Ormerod
Today, there are an estimated 400,000 electric vehicles (EVs) on the roads of Britain. And there are over three quarters of a million plug-in hybrids (PHEVs).
Today, there are an estimated 400,000 electric vehicles (EVs) on the roads of Britain. And there are over three quarters of a million plug-in hybrids (PHEVs).
Electric vehicles aren’t the future, they’re the present. They’re expected to outsell diesel cars by the end of this year. It’s a seismic shift in the automotive market, with knock-on effects for drivers, repairers, and insurers.
And a seismic shift is just what you don’t need in the middle of a perfect storm.
Even without Covid, without Brexit, without semiconductor shortages and a repair brain drain, the switch to electric would throw up all sorts of challenges. Challenges that demand a certain kind of expertise.
So Kirsty’s tracked down an EV expert. Mark Ormerod, a director at Gillibrands, a huge proponent of EV safety, and of course - an exceptional repairer.
When it comes to the electrical issue exacerbating the perfect storm, Mark knows his stuff.
“This should’ve been in place before the cars were released.”
Cogent Hire has built a network of EV experts to meet the challenges of a move to electric vehicles - because we saw the way the market was moving.
But when you listen to Mark, you realise that not everyone was quite so forward-thinking.
“Everyone’s talking EV. 23, 24% of vehicles in the UK are electric. And that’s causing problems.”
The problem isn’t with the vehicles - it’s with the infrastructure. We’re not talking about charging stations here, Mark means the repair and maintenance infrastructure that keeps over a million electrically-powered vehicles on the road.
“Everything should have been in place before the cars were released. There were obvious questions to ask.”
“Have we got a network of repairers to repair these cars? Who is going to repair them? Where are they going to be repaired? How complex will that be? Who is going to train the technicians, and who is going to fund it?”
“We know, because we worked it out.”
Electrical vehicles need specialist training
Mark and Gillibrand Blackburn prepared for the huge surge in electrical vehicles by investing in training and manufacturer equipment - ensuring that their repairers had the skills and the knowhow to service these complex machines.
But even with the right amount of foresight and planning, the perfect storm has struck. And a lack of training facilities is leading to a shortage of expertise and delays in repairs.
Especially because electric vehicles are complex. The old skillsets aren’t always applicable, and to repair EVs safely, you need to undertake vehicle manufacturer approved training.
So what happens if those training centres close down?
“The difficulties we’ve had in the last 12 months have mainly been around training, and that’s due to Covid.”
“They just shut the training centres down temporary due to covid, basically, so the first half of last year meant the training centres were playing catch-up, which was very, very expensive and caused production problems with countless courses to catch up on.”
“In three years time, we’re going to have the exact same problem because all the required training is going to be crammed into a very short period as quite a lot of these courses expire after three years and you have to be re-accredited.”
A lack of training facilities means it’s harder for repairers to educate staff. But it’s not stopped Mark from educating another very important audience.
“In the last twelve months we’ve spent time trying to educate segments of the industry which have included insurance companies and engineering companies by running EV and ADAS training days free of charge. We have done this to engage with a wider audience, to let them know how electrical vehicles have changed the way we work. Because there needs to be an adjustment..”
It’s not just electrics. It’s electronics.
Part of the adjustment needed goes beyond electrical cars. Because even petrol vehicles are now packed with electronics. The old ways of repairing vehicles no longer apply, and that means the old expectations from insurers no longer apply either.
It’s all down to on-board diagnostic technology, and that’s technology that you can only access and use with the right - vehicle manufacturer approved - equipment.
It makes an already tough job even tougher, as Mark explains.
“The methodology now all comes from the diagnostics systems. You need to plug into the on board diagnostics, and you end up with a specific repair methodology.”
“You can do anything with this computer. You can do calibrations, you can reprogram items, but everything is specific to that vehicle - to that chassis number.”
“You can take four vehicles from the same year, with the same type of engine, and suddenly there will be two or three variations on how you carry out certain procedures.”
Even more challenging, these procedures can change from one day to the next, with software updates and additions. It’s a far cry from repairers learning techniques that will last a lifetime.
“Anything can change on a daily basis. You might get a methodology today for something as straightforward as repressurising a water system, but that doesn’t mean you follow it tomorrow. If the manufacturer isn’t happy, things can change quickly.”
“And that means that things can go wrong on a specific repair, even though you’ve followed the same procedure as yesterday.”
With changes this swift, and this regular, it’s no wonder there are so many delays to electrical repairs. Mark sums the whole situation up in a way we can’t help but agree with.
“It’s quite bizarre.”
This complexity contributes to delays, but isn’t there a simple solution out there?
Increasing complexity needs a solid strategy
Even with training centres re-opened following the pandemic, you can’t become a VM-approved EV repair expert overnight. Vehicles will continue to become more complex, training will continue to become more demanding, and it’ll take longer to reach the skill levels required.
The only way to solve this problem in the future is to start preparing and acting now.
“If repairers don’t have a future plan and don’t understand their direction of travel - even if they know where they want their business to be, they won’t have the people to do it.”
“It’s got to be a gradual process. Because if you’re not repairing cars, you’re not paying the bills. But you need to train your people. We’ve managed to do it, over a number of years, very, very gradually, and now we’re comfortable that technicians we’ve been training for a number of years can now work safely on a modern day car to protect everybody’s interests.”
“It’s working for us.”
Mark’s advice to repairers is clear. If you want to survive the perfect storm and thrive once it’s blown over, you need to get ahead of the curve. Upskill quickly, and let everyone know that times have changed.
It’s more important than ever for everyone to understand the issue
Communication. It’s clear from Kirsty’s chat with Mark that communication needs to improve.
“There’s this massive delay, and we’re trying to minimise it. To say it’s alright. We need to be clear that things are taking more time, and that prices are going up. Charging £75 for a diagnostics check isn’t the answer on most modern day cars, What is more important is understanding the car and researching the correct methodology and re-learning and recalibrating the systems on the vehicle that have been affected by the accident or the repair procedure.”
“We need to be clear.”
Transparency between repairers, drivers and insurers. That’s something Cogent Hire will keep championing even after the perfect storm has blown over.